

Celebrating 22 Years as a CNC Systems Integrator
Machine Tool
Retrofits & Rebuilds
Since our founding in 2003, we have successfully completed over 350 CNC retrofit and rebuild projects across virtually every type of machine tool. We provide service throughout the continental United States, offering Fanuc, Siemens, and NUM control systems to meet your specific requirements.
Our Expertise
Breathing New Life into Legacy Machine Tools
CNC Retrofits
Our retrofit solutions include high-end digital CNC systems, cost-effective analog control upgrades, and DIY CNC retrofit kits. Analog retrofits allow you to keep your existing drives and motors while upgrading the control systems. In contrast, digital systems replace all components, providing maximum reliability and ease of service.
PLC Upgrades
Upgrade your relay or outdated PLC machines to enhance up-time and ease of use. A modern control system can eliminate failures stemming from obsolete electrical components, providing improved performance for applications that don’t need the full capabilities of a CNC system.
Drive Replacements
We provide cost-effective drive replacement solutions for AC and DC motors across various applications, allowing customers to upgrade their old drive systems without fully replacing them. Additionally, we offer new motors when needed to ensure optimal performance.
Hydraulic Solutions
We provide cost-effective hydraulic solutions for machine tool applications, avoiding expensive system replacements. Our Delta Computer Systems Hydraulic Controllers enable precise control of hydraulically operated axes, offering an efficient alternative that meets our customers' needs.
Mechanical Rebuilds
We offer mechanical rebuilds, field services, precision scraping, and alignment & installation. While we don’t provide in-house mechanical services, we can refer trusted partners and manage projects with both mechanical and electrical components to ensure they stay on schedule and within budget.
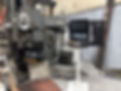

Why Choose Us?
We forge true partnerships with our customers, not merely transactional relationships. Your success directly powers our own, which is why we're relentlessly committed to delivering retrofit projects that meet both your timeline and budget requirements—without ever compromising on quality or performance.

Turnkey Solutions
Just supply us with your application requirements. We'll handle everything from system design to commissioning and operator training.

Experienced Integrators
Our most senior Controls Engineer has over 30 years of CNC retrofit experience. There's simply no project we can't handle.
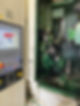
Vendor Selection
We've spent decades carefully curating our vendor selection to ensure you receive not only the best technology but also access to a reliable spare parts and service network.

Onsite Services
You don't need to move your machine for a control retrofit or mechanical rebuild. Almost all our work can be done onsite, so you can avoid the hefty moving bill.